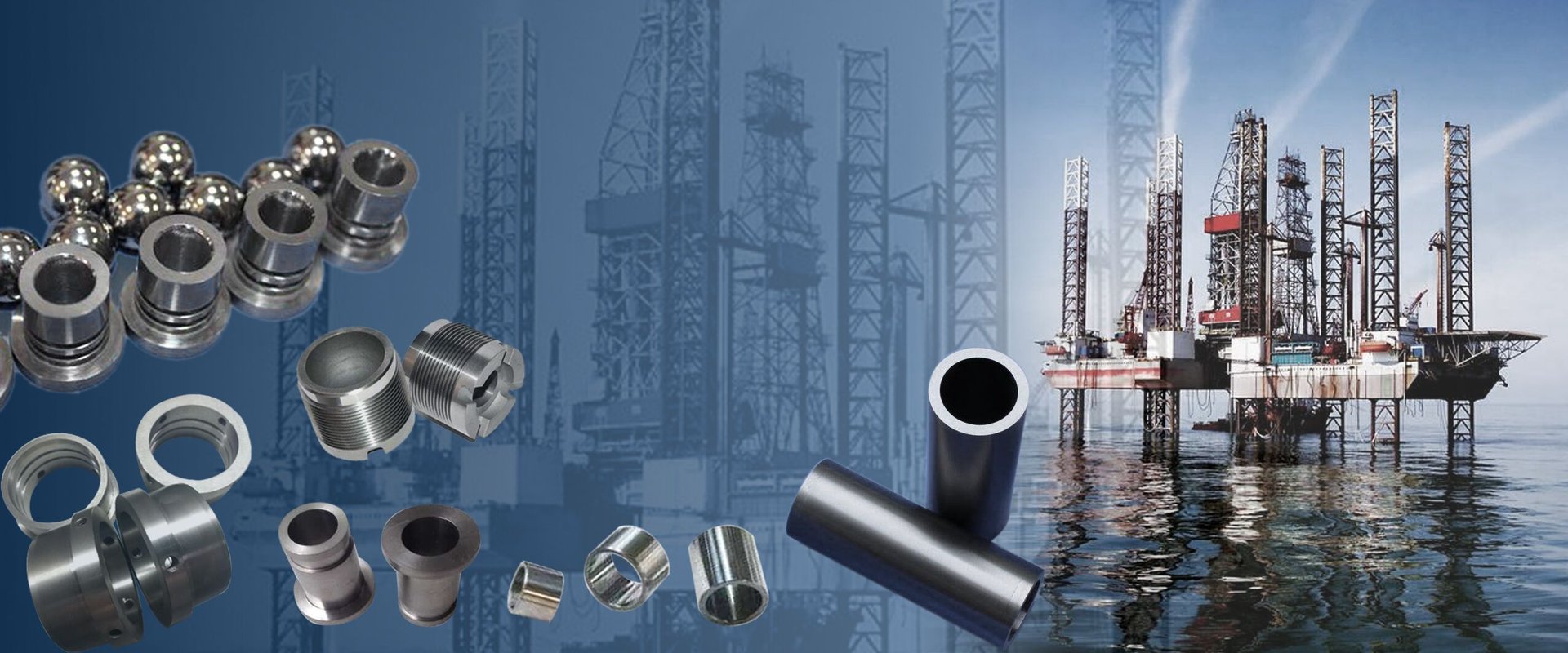
Wear Less, Achieve More with Tungsten Carbide
Expertly designed wear-resistant parts for your needs. Precision manufacturing and personalized service.
Tungsten Carbide Hardfacing Rod
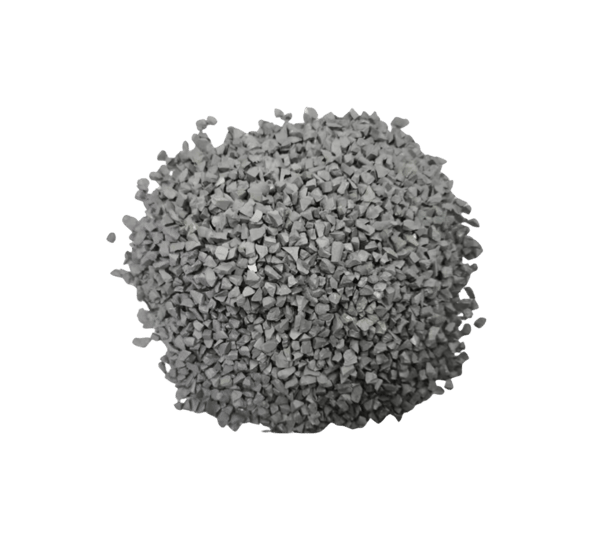
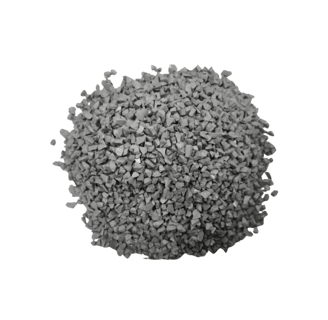
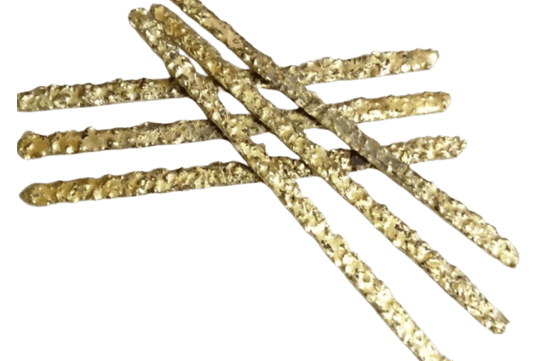
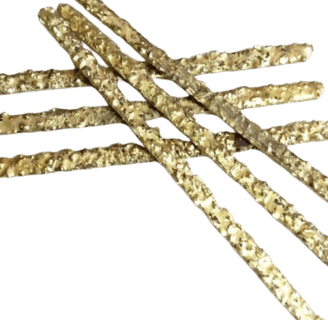
John Doe
Tungsten Carbide Rod with Fluxed
Tungsten Carbide-Nickel Composite Rod (WC-Ni)
YD cemented carbide composite surfacing electrode is made of sintered tungsten carbide grit and flexible base metal. It is coated with a special flux and colored to identify the particle size. The sintered cemented carbide particles are mainly cobalt-containing tungsten carbide, the hardness is HRA89-91, the matrix metal is "nickel-copper" alloy, the tensile strength is 690Mpa, and the hardness is HB≥160
The YD type electrode needs to be used in conjunction with a base electrode (YD-D) and a special flux (YD-R). The YD-D base electrode is a gas welding electrode with a special flux coated on the outer skin. The amount should be the weight of 15% of the YD electrode.
YD-R is a compound flux, and the amount should be 2% of the weight of the YD electrode
Applications of Tungsten Carbide-Nickel (WC-Ni) Composite Rod:
Mining and Drilling
Drill Bits: Used in ore drilling and oil drilling. Its high wear resistance and corrosion resistance enable it to maintain performance in harsh working environments.
Impact Tools: Utilized in geological exploration and mining impact tools, capable of withstanding high impact loads due to its good strength and wear resistance.
Oil and Gas Extraction
Drilling Tools: Employed in oil and gas drilling operations. The tungsten carbide-nickel composite rod offers enduring durability in high-temperature, high-pressure, and corrosive environments.
Packers Components: Provides wear and corrosion resistance in packers and other equipment, protecting critical components.
Industrial Applications
Wear Parts: Used in various industrial equipment, such as crushers and conveyors. Its wear resistance allows it to maintain a long service life in high-wear environments.
High-Load Components: Designed for components that bear significant loads, offering high strength and stability.
High-Temperature and High-Pressure Applications
High-Temperature Equipment Components: Suitable for manufacturing and processing in high-temperature environments, such as high-temperature furnaces and heat treatment equipment, due to its excellent thermal stability and wear resistance.
Surfacing Process
The YD type electrode adopts oxygen-acetylene flame for surfacing welding, and the gas welding tip should be larger than that of ordinary gas welding carbon steel. The flame should be adjusted to a neutral or slightly carbonized flame. The position of the neutral flame core should be strictly controlled, and it should not touch the cemented carbide particles and the surface of the workpiece to avoid over-burning, which is higher than the tips of ordinary gas welding, it’s the key to surfacing layer’s wear life.
The flat welding position should be used as much as possible when surfacing welding, and suitable molds should be used for surfacing welding in other positions
The workplace must be well ventilated to avoid harmful health
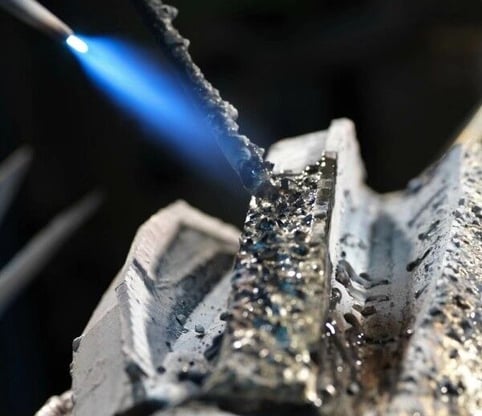
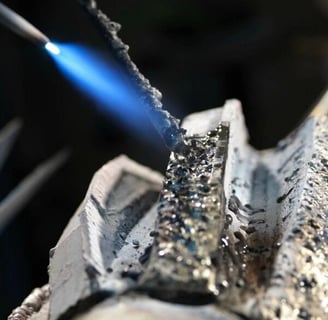
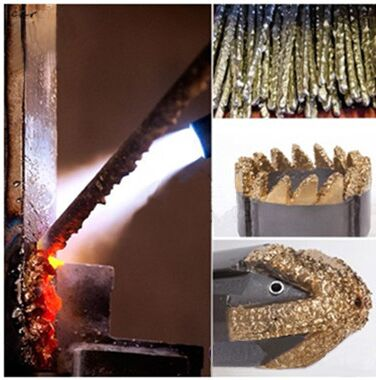
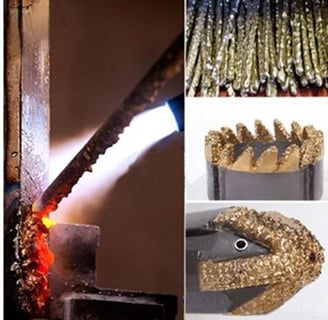
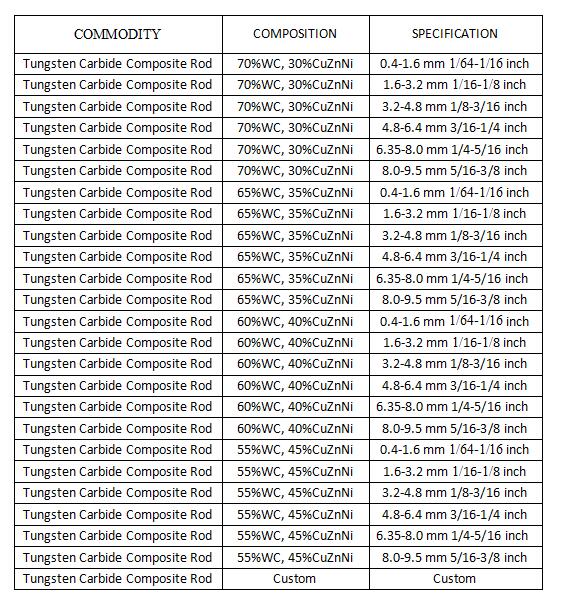
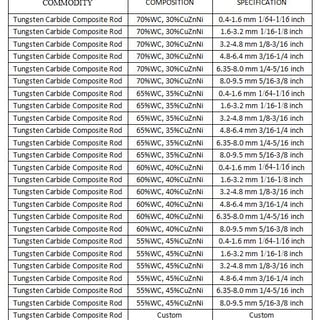
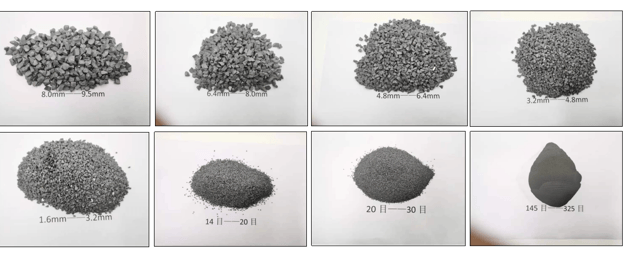
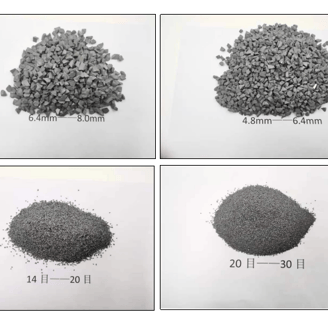
Regular Specification
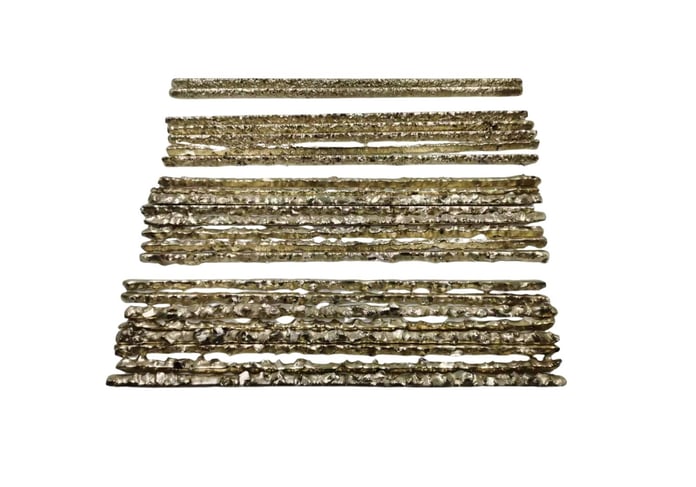
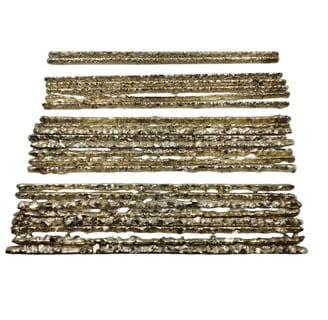