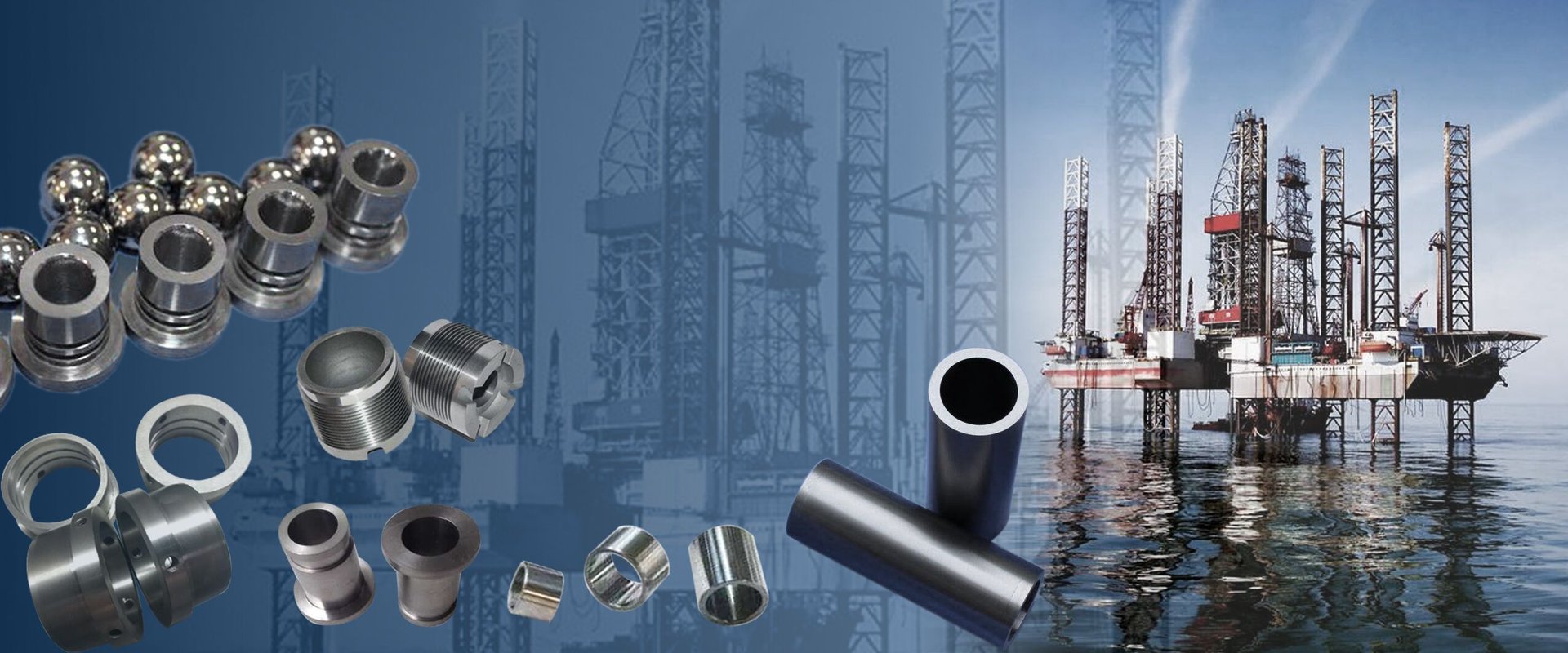
Wear Less, Achieve More with Tungsten Carbide
Expertly designed wear-resistant parts for your needs. Precision manufacturing and personalized service.
Tungsten Carbide Sleeve
Extensive Range
-Standard Cylindrical Sleeves
-Grooved Cylindrical Sleeves
-Bossed Sleeves
-Grooved Bossed Sleeves
-Non-standard Sleeves
We offer a vast selection of sizes and types to cater to diverse needs
Furthermore, we can recommend, design, develop, produce, and supply products tailored to customers' specific drawings and requirements.
★★★★★
Carbide Sleeve
1. Protective Sleeve
Protective Sleeves are used to protect equipment surfaces from wear, corrosion and erosion, thereby extending the life of the equipment and reducing the need for maintenance. In the oil and gas industry, Protective Sleeves are widely used on drill bits, drill pipe and wellhead equipment to prevent damage to equipment due to the harsh drilling environment and high pressure conditions. In mechanical equipment, such as conveyor belts and gears, these sleeves protect the exterior of the equipment from wear and corrosion during operation, ensuring that the equipment remains in good condition. Additionally, in pumps and valves, protective sleeves prevent corrosion of the equipment by fluids, ensuring long term stable operation and sealing performance.
2. Guide Sleeve
The Guide Sleeve is used to precisely guide and align moving parts to ensure the accuracy and stability of the equipment. It provides smooth movement by reducing friction between parts, preventing deflection and inaccurate alignment. In CNC machine tools and machining centers, guide sleeves help ensure precise alignment of tools or workpieces during machining, improving machining accuracy. In automated equipment and robotic systems, it guides the stable operation of moving parts such as robotic arms and conveyor systems. In conveyor systems, guide sleeves ensure smooth and accurate positioning of materials during transportation.
3. Seal Sleeve
Seal Sleeves are used to form a seal between mechanical components to prevent leakage of fluids (such as oil, gas or water) and to work effectively in high pressure, high temperature or corrosive environments. In pumps and compressors, the sealing sleeve forms a seal between the pump body and compressor housing, preventing fluid leakage while withstanding pressure and temperature changes within the equipment. In valves, it prevents fluid leakage from inside the valve, ensuring fluid control accuracy and system safety. In addition, sealing sleeves are used in chemical equipment to prevent chemical leakage and protect the operating environment and equipment.
4. Wear Sleeve
Wear Sleeves are used to withstand and resist highly abrasive environments, protecting equipment from wear and impact. It is used in mining equipment (such as crushers and screens) to withstand the wear and tear of ore and rock, reducing the frequency of equipment repair and replacement. In agricultural machinery, such as tractors and combines, wear sleeves reduce wear and tear when handling soil and crops, enhancing equipment life. In manufacturing equipment, such as grinders and milling machines, wear sleeves reduce wear during machining, keeping production lines running efficiently.
5. Fluid Control Sleeve
Fluid Control Sleeves are used to regulate and control the flow, pressure or direction of fluids to ensure stability and accuracy of fluid flow. In the oil and gas industry, the Fluid Control Sleeve regulates the flow and pressure of oil and gas in wellhead equipment and blowout preventers to ensure safe operation and productivity. In injection systems, it regulates the direction and speed of fluid injection to ensure uniform spraying and efficient treatment processes. In chemical equipment, fluid control sleeves are used to control fluid flow during chemical reactions to ensure stable reaction conditions and product quality.
Application Areas
Oil & Gas: Protects drilling tools and wellhead equipment from wear and corrosion.
Mechanical equipment: for external protection of components such as conveyor belts, gears and drums.
Mining and quarrying: to withstand high abrasion and impact in crushers and screens.
Metallurgy: protects equipment such as furnaces and converters against high temperatures and chemical corrosion.
Aerospace: protects aerospace devices by withstanding high pressures and temperatures.
Chemical and Pharmaceutical: protects equipment by handling corrosive and high temperature chemicals.
Food processing: Providing wear protection in processing equipment to ensure food safety.
Paper and Printing: Reduces wear and tear on production equipment and improves productivity.
High-quality tungsten carbide sleeve tailored to your specifications
Discover our versatile tungsten carbide sleeves, engineered for exceptional performance and tailored to meet diverse industrial applications. Whether you need a protective sleeve to shield equipment from damage, a guide sleeve for precise alignment, a seal sleeve to prevent leakage, a wear sleeve for enhanced durability in harsh conditions, or a fluid control sleeve to manage and optimize flow, our products are designed to deliver outstanding results. Each sleeve is crafted from high-quality tungsten carbide, ensuring superior strength and longevity. Our bespoke solutions allow for customized specifications to perfectly fit your unique operational needs, providing you with the ultimate in reliability and efficiency.
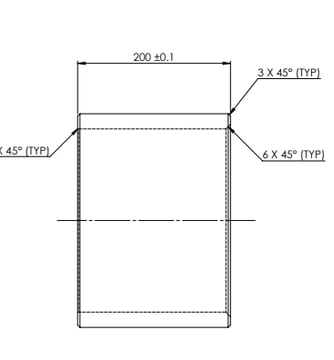
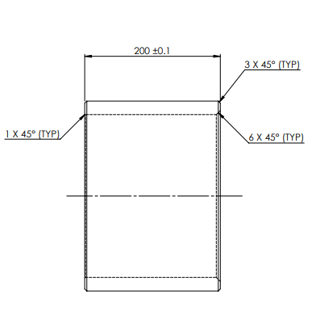
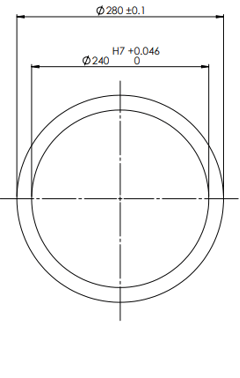
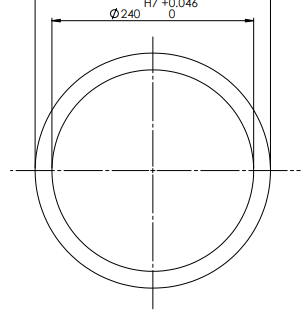