Which Tool Do You Use Most with Tungsten Carbide: End Mills or Rods?
weisoncarbide
11/22/20243 min read
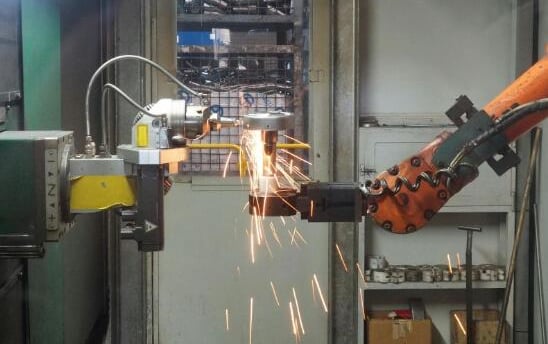
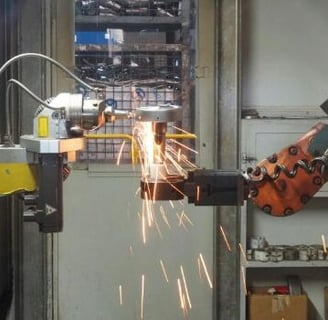
Overview of End Mills: Types and Uses
End mills are crucial tools in the machining industry, widely utilized for various cutting applications. They are designed to remove material through rotary cutting and are available in several types, each tailored for specific tasks. The three most common varieties are flat end mills, ball-nose end mills, and corner radius end mills. Each type serves a unique purpose in machining, contributing to the versatility and effectiveness of the tools.
Flat end mills are characterized by their straight cutting edges, which make them ideal for producing flat surfaces and creating slots. Their straightforward design also allows for effective plunging into workpieces, making them a common choice for basic milling operations. Conversely, ball-nose end mills possess a rounded tip that enables the creation of contoured surfaces, allowing for more intricate shapes and complex three-dimensional designs. This type is particularly advantageous in applications requiring a high degree of precision, such as in mold making and detailed engraving.
Corner radius end mills, which feature a small radius at the corners, strike a balance between flat and ball-nose end mills. They are perfect for reducing the risk of chipping and wear when machining corners, thus enhancing tool longevity while providing a cleaner finish compared to their flat counterparts. These tools are frequently employed in highly demanding applications where rounded edges or tight spaces pose challenges.
The advantages of using end mills extend beyond their shapes. Their ability to create precise cuts allows for the efficient production of complex parts with minimal material wastage. They find applications in various industries, such as aerospace, automotive, and general manufacturing. With their diversity in design and functionality, end mills remain a fundamental component in the toolkit of machinists and engineers alike.
Exploring Tungsten Carbide Rods: Characteristics and Benefits
Tungsten carbide rods are a vital component in the manufacturing of cutting tools and wear parts due to their impressive hardness and wear resistance. These rods are composed primarily of tungsten carbide particles bound together by a metallic binder, typically cobalt. This unique structure grants tungsten carbide rods excellent mechanical properties, allowing them to maintain their shape and sharpness even under high-stress conditions. Unlike end mills, which are specifically designed for rotary cutting applications, tungsten carbide rods offer a versatile solution that can be machined into a variety of shapes, making them an indispensable material in toolmaking.
The manufacturing processes for tungsten carbide rods typically involve powder metallurgy techniques. In this method, tungsten carbide powder is mixed with a binder and then pressed into a desired shape, followed by sintering at high temperatures. This process results in a dense, hard material that is capable of withstanding extreme wear. Once the rods are produced, they can be further machined or ground to achieve specific dimensions and tolerances, which are critical for their end applications.
The benefits of using tungsten carbide rods extend beyond their hardness. Their resilience to heat and corrosion makes them suitable for use in various industries, such as automotive, aerospace, and mining. In comparison to end mills, tungsten carbide rods are often preferred in applications where high precision and durability are required. For instance, they are commonly used to produce cutting tools, blanks, and wear parts, where their robust characteristics can enhance the performance and lifespan of the final product. Furthermore, in certain scenarios, tungsten carbide rods can be custom-shaped or ground to create specialized tools that address specific machining challenges.
Making the Choice: End Mills vs. Rods for Your Project
When it comes to selecting between end mills and tungsten carbide rods, a variety of factors must be considered to ensure optimal tool performance based on specific project requirements. Each tool plays a distinct role in machining processes, and understanding their strengths is essential for making informed decisions.
End mills are versatile cutting tools designed primarily for milling operations. They excel at removing material from a workpiece, allowing for intricate shapes, profiles, and contours. This characteristic makes them highly suitable for projects that demand precision, such as creating detailed components or complex geometries. End mills are available in various configurations, including square, ball, and corner radius options, which further enhances their adaptability to different applications.
On the other hand, tungsten carbide rods serve as foundational materials for manufacturing cutting tools or as shafts for drilling applications. Their primary advantage lies in their hardness and resistance to wear and deformation, making them ideal for high-performance tools. When the task at hand focuses on developing or reinforcing tools, tungsten carbide rods emerge as the suitable choice due to their superior durability.
Budget considerations are also pivotal in the decision-making process. Although tungsten carbide tools generally offer longevity and efficiency, they may entail a higher initial investment. Conversely, end mills can be more cost-effective for projects where multiple cuts are required, especially if the scope can justify the operational expenditure.
In practical scenarios, industry professionals often recommend assessing the material type and project scale before choosing the appropriate tool. For example, in cases involving softer materials, end mills may prove advantageous, while more robust machining tasks might require the strength of tungsten carbide rods. By considering these factors, you can effectively optimize your tooling choices and enhance project outcomes.
Quality
a
© 2024. Weison Tungsten All rights reserved. sitemap carbide tools for sale
Industry
Follow us
Tian District , Zhuzhou Hunan, China
Address: No.8 Dahan Huipu Industry
412000
Phone:0086 22105289
Email:info@weisontungsten.com