The Complete Guide to Increasing Manufacturing Efficiency Using Carbide Tools
weisoncarbide
10/25/20245 min read
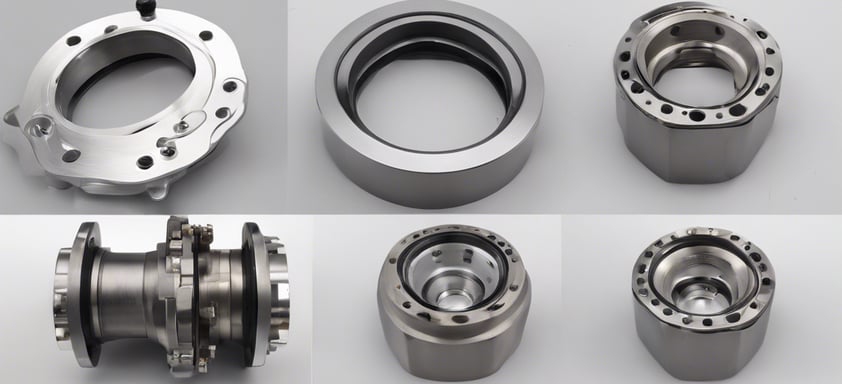
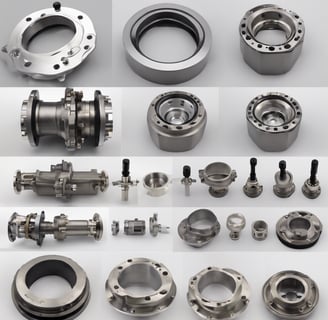
Understanding Carbide Tools and Their Benefits
Carbide tools are essential components in modern manufacturing processes, known for their high performance and longevity. These tools are typically made from tungsten carbide, a composite material that is extremely hard and durable. The unique properties of carbide, including its hardness, resistance to wear, and ability to withstand high temperatures, make it an ideal choice for cutting, grinding, and milling operations. Compared to traditional steel tools, carbide tools offer significant advantages in terms of efficiency and precision.
One of the most notable features of carbide tools is their hardness. On the Mohs scale of mineral hardness, tungsten carbide ranks around 9, making it one of the hardest materials available for tooling. This attribute allows carbide tools to maintain their cutting edges for a longer duration, reducing the frequency of tool changes and contributing to increased productivity on the shop floor.
In addition to hardness, carbide tools exhibit excellent resistance to wear and thermal expansion. This means that they can perform reliably under high-stress conditions, where conventional tools might fracture or deform. With less wear over time, manufacturers benefit from lower operational costs, as fewer replacements are required, which translates into reduced downtime.
There are various types of carbide tools available in the market, including end mills, drill bits, inserts, and saw blades, each designed for specific applications. The diverse range of carbide tools allows manufacturers to select the most suitable tool for their specific operations, ensuring optimal results. When compared to tools made from materials such as high-speed steel (HSS) or cobalt, carbide tools often outperform in cutting speed, material removal rates, and overall efficiency.
Thus, leveraging carbide tools in manufacturing processes leads to enhanced precision, minimized downtime, and overall cost-effectiveness. As industries continue to seek ways to improve efficiency, the adoption of carbide tools has become increasingly attractive for manufacturers aiming to enhance their operational capabilities.
Key Strategies for Implementing Carbide Tools in Manufacturing
Integrating carbide tools into manufacturing processes requires a systematic approach that encompasses several critical strategies. The first step is to conduct a thorough assessment of the current tooling systems employed within the manufacturing operation. This assessment should identify inefficiencies, tool wear patterns, and areas where carbide tools might significantly enhance production capabilities. Understanding these factors will not only inform the selection of the most appropriate carbide tools but also instigate potential process redesigns to optimize overall efficiency.
Once the assessment is complete, selecting the right carbide tools for specific operations becomes paramount. It is crucial to analyze the material being worked on, the required precision of the task, and the expected production volume. Using carbide tools that possess superior wear resistance and toughness can lead to extended tool life, reduced downtime, and increased productivity. Manufacturers should consider collaborating with tool suppliers to gain insights into the latest developments in carbide technology and to understand which tools best fit their operational needs.
Moreover, training employees on the effective usage of carbide tools is essential in maximizing their operational benefits. Well-trained staff can appropriately select the correct tool for specific jobs, ensuring optimal performance and reducing the likelihood of errors. Regular workshops and hands-on training sessions can facilitate knowledge transfer and keep the team updated on best practices for handling carbide tools safely and effectively.
In addition to training, implementing best practices for tool management, maintenance, and storage is crucial. Proper storage conditions can prevent damage and degradation of carbide tools, thereby maximizing their lifespan and maintaining performance. Establishing a routine maintenance schedule will ensure that tools are kept in excellent condition and ready for production demands. Real-world examples across various industries display the effectiveness of these strategies, illustrating how companies have successfully enhanced their manufacturing efficiency through the strategic deployment of carbide tools.
Measuring and Analyzing Manufacturing Efficiency
Accurately measuring manufacturing efficiency is crucial for organizations looking to enhance their productivity after transitioning to carbide tools. One effective way to assess efficiency gains is through establishing key performance indicators (KPIs) that can provide meaningful insights into operational performance. Key metrics include cycle time reduction, scrap rate, and overall equipment effectiveness (OEE).
Cycle time refers to the total time taken from the beginning to the end of a manufacturing process, providing a clear indication of how quickly production occurs. By analyzing cycle times before and after the adoption of carbide tools, manufacturers can quantify the impact on efficiency. A lower cycle time indicates improved speed and productivity, which is pivotal to enhancing overall efficiency.
The scrap rate is another crucial KPI, representing the percentage of materials that are wasted during production. Lowering the scrap rate is essential for reducing costs and improving profitability. Organizations can monitor changes in scrap rates following the implementation of carbide tools, thereby assessing improvements in precision and quality.
OEE is a comprehensive measure that accounts for machine availability, performance, and quality. By focusing on OEE, manufacturers can identify areas that require improvement, enabling them to optimize processes further. Many software solutions and analytical tools specifically designed for manufacturing provide robust data collection and analysis capabilities. These tools can streamline the monitoring of KPIs, making it easier for manufacturers to spot trends and make data-driven decisions.
Continuous improvement should be at the forefront of any successful manufacturing strategy. Regularly reviewing performance metrics and making necessary adjustments fosters an agile environment, allowing organizations to adapt to changing market demands and technologies rapidly. In a landscape characterized by constant advancements, maintaining efficiency through diligent measurement and analysis is imperative for long-term sustainability.
Future Trends in Carbide Tool Technology
The landscape of manufacturing efficiency is continually evolving, especially with the advent of innovative carbide tool technologies. One of the primary trends shaping the future is the development of advanced coatings for carbide tools. These coatings enhance properties such as wear resistance, reducing tool wear and extending tool life. As manufacturers aim for higher productivity rates, the focus on creating specialized coatings that cater to specific applications is increasing, allowing for more effective machining processes with fewer tool changes.
Additionally, innovative insert designs are emerging as a significant factor in enhancing carbide tool efficiency. The design improvements aim at optimizing chip removal and heat dissipation, which ultimately leads to better machining performance. Manufacturers are also exploring geometries that facilitate higher feed rates and speeds, aligning with the goals of minimizing cycle times and maximizing output. This ongoing research in insert technology is crucial, as it aids manufacturers in meeting the rigorous demands of modern production environments.
Another transformative trend is the incorporation of smart technology within carbide tools. The rise of Industry 4.0 has brought forth advanced automation technologies and data analytics. Carbide tools embedded with sensors can provide real-time feedback on tool performance, allowing for predictive maintenance and reducing unplanned downtime. This integration of smart technology helps manufacturers make informed decisions that optimize operations and contribute to a leaner production process.
Moreover, as sustainability becomes increasingly important in manufacturing, the development of carbide tools is also focusing on eco-friendly practices. Innovations such as re-sharpenable tools and the use of sustainable materials contribute to reducing waste and improving resource efficiency. By embracing these emerging trends in carbide tool technology, manufacturers can significantly enhance manufacturing efficiency while adhering to sustainable practices, ultimately ensuring competitiveness in a rapidly changing market landscape.
Quality
a
© 2024. Weison Tungsten All rights reserved. sitemap carbide tools for sale
Industry
Follow us
Tian District , Zhuzhou Hunan, China
Address: No.8 Dahan Huipu Industry
412000
Phone:0086 22105289
Email:info@weisontungsten.com